- WATERJET LOOMS WEAVING TECHNOLOGY
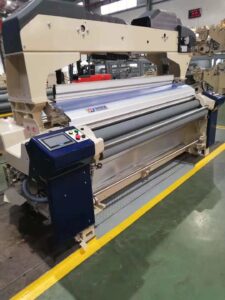
Water jet weaving involves weaving on a water jet loom, which is similar to an air jet loom but uses water instead of air to transport the yarn around the shed. Water jet looms can weave quickly without damaging the yarn, as water is less abrasive than solid matter, such as in rapier weaving looms. Water jet weaving is suitable for yarns of hydrophobic nature like Polyester PET, Acetate CA, or Polyamides. However, it is not suitable for hydrophilic materials like cotton, nettle, or hemp, as they would become too heavy due to extreme moisture absorption during weaving.
During water jet weaving, a significant amount of water is consumed, and industries with 50 to 150 machines can result in substantial water wastage. The wastewater from water jet weaving contains cutting oil present in the yarn, primarily emulsified oil and yarn string, which require specific treatment for textile water.
- PRE-SCREENING FOR DRAINAGE
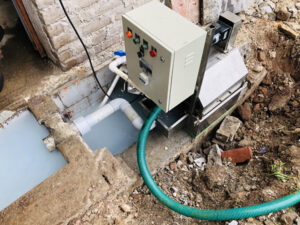
In textile waterjet looms, a pre-screening process is essential to remove yarn shade. Without pre-screening, the collection tank with the drain pipe gets clogged with yarn shades, oil, and grease, leading to operational issues. Installing an automatic rotating drum system for pre-screening can remove micro yarn shades before they enter the collection tank, saving on operation costs, manpower, and preventing drainage pipe blockages.
- DAF SYSTEM FOR WATERJET LOOMS
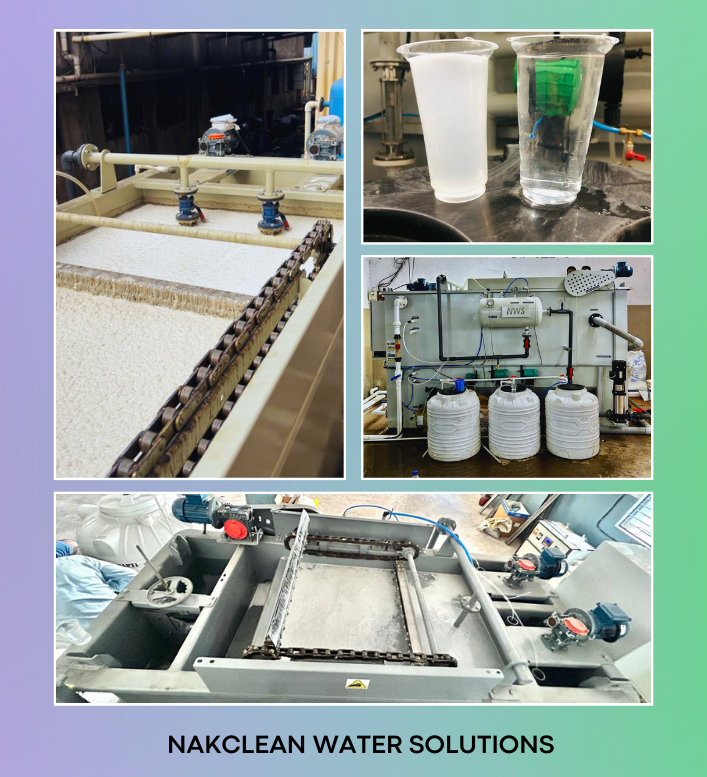
Furthermore, the Dissolved Air Flotation (DAF) system is a perfect solution for eliminating dissolved emulsified oil present in wastewater from water jet looms. It can reduce the emulsified oil content from 100-800 ppm to lower than 10 ppm, thanks to advanced coagulation and flocculation systems that work with chemical-saving technology. After the DAF system, water passes through micro and sand filters, providing clear water for reuse in production. This system can treat wastewater ranging from 50 to 2000 KLD and the resulting dry sludge can be used as boiler feed, offering additional benefits.