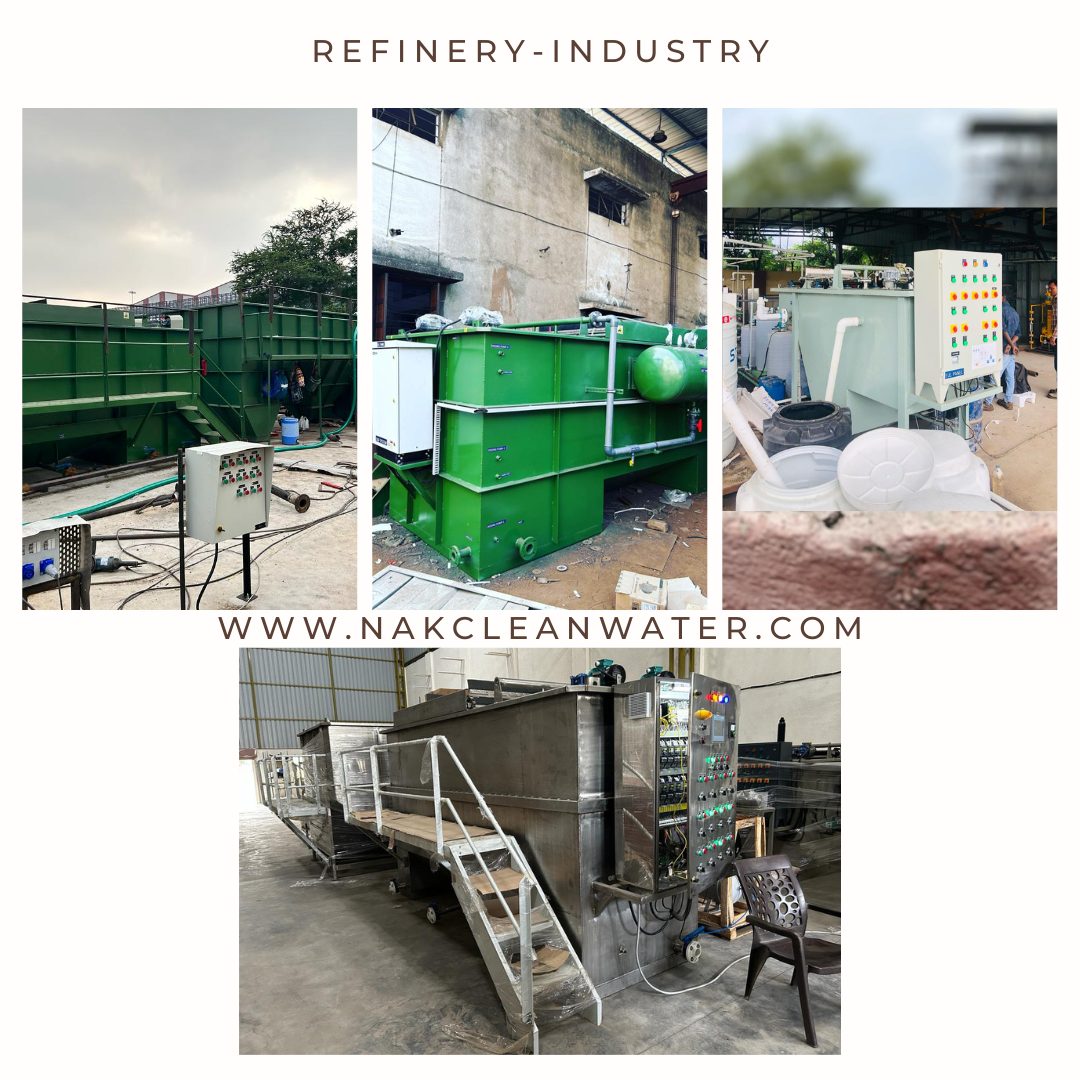
The petrochemical and oil refinery industries are known for their significant environmental impact due to their high pollutants and water consumption. These facilities are typically situated near water sources such as rivers, lakes, and seas for their water supply and discharge needs.
While the petrochemical industry adheres to strict environmental controls, the potential for spills and leaks remains a concern. As a result, petrochemical plants are required to have efficient effluent treatment systems to mitigate pollution.
Similarly, oil refineries often operate on-site water treatment plants to manage the environmental impact of their waste effluents. These plants employ various physical, chemical, and biological processes to eliminate pollutants from wastewater before releasing it into water bodies or reusing it within the refinery.
Furthermore, in regions with pronounced water scarcity, it is crucial to implement measures for wastewater recovery.
Dissolved air flotation (DAF) is a commonly used wastewater treatment process in these industries for effectively separating contaminants from their effluents. DAF systems achieve high removal efficiency for total suspended solids (TSS), oils, and Chemical Oxygen Demand (COD) present in grease, oil, biological sludge, colored organic matter, and colloidal material. Additionally, DAF can be utilized for sludge thickening or secondary clarification of water from a biological process.
Efficiency of Treatment with DAF Equipment in the Oil Industry
Dissolved air flotation (DAF) is a commonly used wastewater treatment process in petroleum refineries, petrochemical and chemical plants. It is used to separate contaminants from effluents. DAF systems achieve 90 to 95% removal efficiency for TSS and 95 to 99% for oils. They also effectively reduce Chemical Oxygen Demand (COD) found in grease, oil, biological sludge, colored organic matter and colloidal material. DAF can also be used for sludge thickening or for secondary clarification of water from biological treatment.
DAF systems are also employed to refine wastewater after biological treatment. In this case, DAF is used to remove any remaining solids or oil and grease (FOG) that were not removed in the primary treatment stages or as a clarifier for water from biological treatment.
For DAF units to operate efficiently, wastewater must undergo a coagulation-flocculation process before entering the DAF system. A lack of or poor design of this physico-chemical pre-treatment will deteriorate the performance of the DAF unit.
The process of treating wastewater from an oil refinery by dissolved air flotation follows the following steps:
Pretreatment: Refinery wastewater undergoes preliminary treatment steps to remove large solids. The wastewater is then screened to remove any remaining large particles and is usually passed to an API or CPI type pretreatment system to separate most of the easily separated hydrocarbons and oils present, by simple density.
Chemical conditioning: Chemical dosing is used to optimize the pH levels and coagulation/flocculation of the wastewater, improving the performance of the DAF system. Various chemicals such as ferric chloride, aluminum sulfate, and polymers can be used to bind colloidal or finely peptized oils, fats and materials dispersed in the water, depending on the nature of the contaminants present in the wastewater.
DAF operation: The wastewater is pumped into a DAF tank, where it is mixed with recycled wastewater. Compressed air is injected into the tank, causing the formation of micro-bubbles that attach to the flocculated particles, which float to the surface and form a sludge layer.
Sludge removal: The sludge layer on the surface of the DAF tank is swept away by a skimming mechanism and collected in a separate sludge tank for further treatment. The clarified water is then discharged to the next stage of the treatment process.
Conclusion
Wastewater from petrochemical industries contains a high concentration of organic matter and, above all, traces of hydrocarbons, oils and grease. A significant proportion of these materials are in colloidal form (TSS), which requires a chemical conditioning of coagulation/flocculation, with its corresponding pH adjustment, in order to condition them for separation by flotation. The DAF system, and in particular, the equipment provided by NWS-DAF, is specially designed to facilitate the separation and removal of these agents with a high level of efficiency, minimizing the risk of leakage.
Considering the growing trend towards the recovery of wastewater for reuse in industrial services and processes, the role of DAF systems becomes more prominent, as they guarantee a longer and better service life of the filtration membranes used in these purification processes.